When the Boeing 777X twin-aisle passenger jet goes into full production for its debut in 2020, each fuselage will be built using special advanced automation technology, the result of a collaborative effort by the airplane maker and the KUKA Systems Aerospace Group.
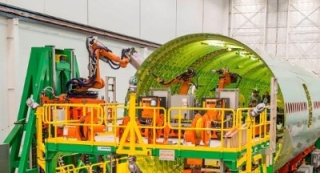
The robotic pulse production line, known as the Fuselage Automated Upright Build (FAUB), will be the baseline manufacturing process for the 777X and prior to that, for assembling fuselages for current 777 models. It's the first time Boeing will use such technology to manufacture wide-body commercial airplanes. The pulse line uses guided KUKA robots equipped with end effectors manufactured by another KUKA company, Alema Automation, to do the riveting currently performed by workers using handheld tools. The robots will work on the forward and aft sections, installing up to 60,000 fasteners per 777 fuselage, quickly and with great precision.
For KUKA Systems, the project is one of the largest it has undertaken in the aerospace sector. The company's roster of current aerospace projects includes the automated assembly of the center fuselage of a new jet fighter, an assembly line for a new super-medium class of commercial helicopter and robotic drilling platforms for a new, long-range business jet. They leverage the expertise in assembly line automation that has made KUKA Systems the largest supplier of production technology to the North American and European automotive industries.